What is Six Sigma?
The term “Six Sigma” refers to a statistical measure of how far a process deviates from perfection. A process that operates at six sigma has a failure rate of only 0.00034%, which means it produces virtually no defects. Six Sigma was formally introduced by Bill Smith, a Motorola engineer, in 1986. Smith noticed that small variations in Motorola’s manufacturing processes were causing defects and quality issues. He proposed a disciplined, data-driven approach to minimize these variations, thereby reducing defects. This approach became the foundation of Six Sigma
What is Six Sigma?
Six Sigma is a rigorous, data-driven methodology designed to improve business processes by systematically eliminating defects, reducing variability, and enhancing overall efficiency. It focuses on achieving high-quality outputs by identifying and removing the causes of errors, thereby reducing waste and ensuring that processes operate as efficiently as possible. The ultimate goal of Six Sigma is to achieve near perfection, with a target of no more than 3.4 defects per million opportunities, which corresponds to a process that operates within six standard deviations (sigma(s)) from the mean. This is achieved by using a structured approach called DMAIC (Define, Measure, Analyze, Improve, Control) to identify and eliminate causes of variation and improve processes.
Six Sigma is a disciplined and data-driven approach widely used in project management to achieve process improvement and minimize defects. It provides a systematic framework to identify and eliminate variations that can impact project performance.
The etymology is based on the Greek symbol “sigma” or “σ,” a statistical term for measuring process deviation from the process mean or target. “Six Sigma” comes from the bell curve used in statistics, where one Sigma symbolizes a single standard deviation from the mean. If the process has six Sigma(s), three above and three below the mean, the defect rate is classified as “extremely low.”
The graph of the normal distribution below underscores the statistical assumptions of the Six Sigma model. The higher the standard deviation, the higher is the spread of values encountered. So, processes, where the mean is minimum 6σ away from the closest specification limit, are aimed at Six Sigma.
What Is Lean Six Sigma?
Lean Six Sigma is a methodology that combines two powerful process improvement techniques: Lean and Six Sigma.
Lean focuses on minimizing waste and maximizing efficiency by identifying and eliminating non-value-adding activities. This involves streamlining processes, reducing defects, improving quality, and optimizing resources to deliver more value with less effort.
On the other hand, Six Sigma is a statistical approach to process improvement that aims to reduce variation and defects by using data-driven decision making. It involves defining, measuring, analyzing, improving, and controlling processes to achieve consistent and predictable results.
By combining the strengths of these two methodologies, Lean Six Sigma provides a comprehensive approach to process improvement that can be applied to any industry or sector. It is widely used in manufacturing, healthcare, finance, and service industries to improve efficiency, reduce costs, and enhance customer satisfaction.
The 5 Key Principles of Six Sigma
The concept of Six Sigma has a simple goal – delivering near-perfect goods and services for business transformation for optimal customer satisfaction (CX).
Goals are achieved through a two-pronged approach:
Six Sigma has its foundations in five key principles:
Key Principles of Six Sigma:
- Customer Focus: Six Sigma places a strong emphasis on understanding and meeting customer needs. The goal is to deliver consistent, high-quality products and services that satisfy or exceed customer expectations.
- Data-Driven Decision Making: It relies heavily on data collection and analysis to make informed decisions. Every stage of the process improvement cycle is supported by accurate data, ensuring that solutions are based on facts rather than assumptions. Ascertain if the data is helping to achieve the goals, whether or not the data needs to be refined, or additional information collected. Identify the problem. Ask questions and find the root cause.
- Process-Centric Approach: Six Sigma views every business operation as a process that can be measured, analyzed, and improved. By focusing on processes rather than isolated tasks, Six Sigma ensures that improvements are sustainable and replicable.
- Proactive Problem Solving: Rather than waiting for problems to occur, Six Sigma encourages organizations to identify potential defects and inefficiencies before they escalate, fostering a culture of continuous improvement by making changes to eliminate variation. Remove the activities in the process that do not add to the customer value. If the value stream doesn’t reveal where the problem lies, tools are used to help discover the outliers and problem areas. Streamline functions to achieve quality control and efficiency. In the end, by taking out the above-mentioned junk, bottlenecks in the process are removed.
- Keep the Ball Rolling
Involve all stakeholders. Adopt a structured process where your team contributes and collaborates their varied expertise for problem-solving. Six Sigma processes can have a great impact on an organization, so the team has to be proficient in the principles and methodologies used. Hence, specialized training and knowledge are required to reduce the risk of project or re-design failures and ensure that the process performs optimally. - Ensure a Flexible and Responsive Ecosystem
The essence of Six Sigma is business transformation and change. When a faulty or inefficient process is removed, it calls for a change in the work practice and employee approach. A robust culture of flexibility and responsiveness to changes in procedures can ensure streamlined project implementation. The people and departments involved should be able to adapt to change with ease, so to facilitate this, processes should be designed for quick and seamless adoption. Ultimately, the company that has an eye fixed on the data examines the bottom line periodically and adjusts its processes where necessary, can gain a competitive edge.
The Six Sigma Methodology
The two main Six Sigma methodologies are DMAIC and DMADV. Each has its own set of recommended procedures to be implemented for business transformation.
DMAIC is a data-driven method used to improve existing products or services for better customer satisfaction. It is the acronym for the five phases: D – Define, M – Measure, A – Analyze, I – Improve, C – Control. DMAIC is applied in the manufacturing of a product or delivery of a service.
DMADV is a part of the Design for Six Sigma (DFSS) process used to design or redesign different processes of product manufacturing or service delivery. The five phases of DMADV are: D – Define, M – Measure, A – Analyze, D – Design, V – Validate. DMADV is employed when existing processes do not meet customer conditions, even after optimization, or when it is required to develop new methods. It is executed by Six Sigma Green Belts and Six Sigma Black Belts and under the supervision of Six Sigma Master Black Belts. We’ll get to the belts later.
The two methodologies are used in different business settings, and professionals seeking to master these methods and application scenarios would do well to take an online certificate program taught by industry experts.
The Six Sigma Process of Business Transformation
Although Six Sigma uses various methods to discover deviations and solve problems, the DMAIC is the standard methodology used by Six Sigma practitioners. Six Sigma uses a data-driven management process used for optimizing and improving business processes. The underlying framework is a strong customer focus and robust use of data and statistics to conclude.
The Six Sigma Process of the DMAIC method has five phases:
Each of the above phases of business transformation has several steps:
Methodologies:
DMAIC PROCESS (for improving existing processes):
- Define: Identify the problem, project goals, and customer requirements.
- Measure: Measure key aspects of current processes by collecting and analyzing data to understand current performance and establish baselines.
- Analyze: Analyze the data in order to identify the root causes of defects or inefficiencies.
- Improve: Improve processes by developing and implementing solutions to address the root causes.
- Control: Implement controls to sustain improvements and monitor the process going forward to avoid errors.
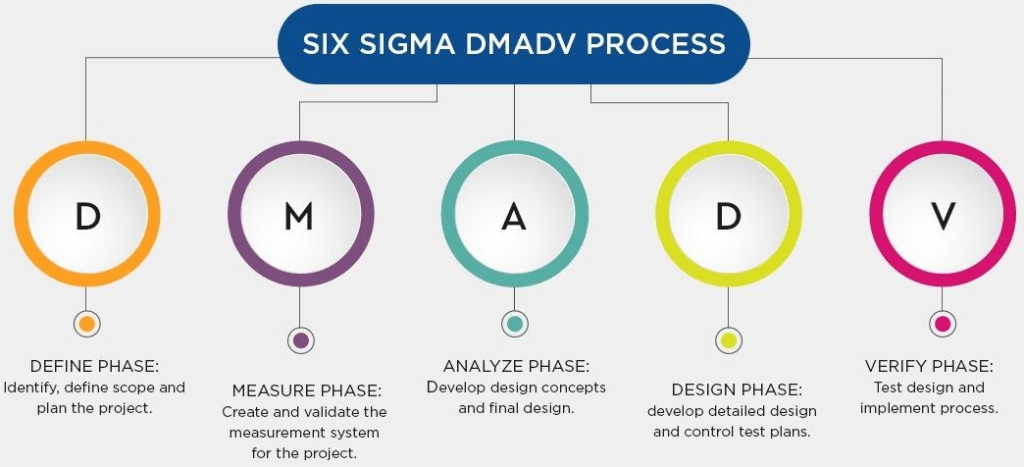
DMADV (for creating new processes or products):
- Define: Define company’s goal(s), set project goals and customer needs for the new process or product.
- Measure: Measure the characteristics Critical To Quality (CTQ) by gathering relevant data and defining key performance indicators (KPIs).
- Analyze: Analyze measurement data, design and optimize the new process or product based on data.
- Design: Design new processes in line with the analysis, develop and test the new process/product to meet the defined requirements.
- Verify: Verify new processes by ensuring that the new process/product performs as expected and delivers the desired results.
Benefits of Six Sigma:
- Improved Quality: By reducing defects and errors, Six Sigma enhances the quality of products and services.
- Cost Reduction: By eliminating inefficiencies, organizations can lower operational costs.
- Increased Customer Satisfaction: Consistent quality leads to higher customer satisfaction and loyalty.
- Enhanced Competitiveness: Streamlined processes make organizations more agile and competitive in the market.
- Employee Engagement: Six Sigma fosters a culture of accountability and continuous improvement, encouraging employees to take ownership of quality.
Six Sigma Techniques
The Six Sigma methodology also uses a mix of statistical and data analysis tools such as process mapping and design and proven qualitative and quantitative techniques, to achieve the desired outcome.
A. Brainstorming
Brainstorming is the key process of any problem-solving method and is often utilized in the “improve” phase of the DMAIC methodology. It is a necessary process before anyone starts using any tools. Brainstorming involves bouncing ideas and generating creative ways to approach a problem through intensive freewheeling group discussions. A facilitator, who is typically the lead Black Belt or Green Belt, moderates the open session among a group of participants.
B. Root Cause Analysis/The 5 Whys
This technique helps to get to the root cause of the problems under consideration and is used in the “analyze” phase of the DMAIC cycle. In the 5 Whys technique, the question “why” is asked, again and again, finally leading up to the core issue. Although “five” is a rule of thumb, the actual number of questions can be greater or fewer, whatever it takes to gain clarity.
C. Voice of the Customer
This is the process used to capture the “voice of the customer” or customer feedback by either internal or external means. The technique is aimed at giving the customer the best products and services. It captures the changing needs of the customer through direct and indirect methods. The voice of the customer technique is used in the “define’ phase of the DMAIC method, usually to further define the problem to be addressed.
D. The 5S System
This technique has its roots in the Japanese principle of workplace energies. The 5S System is aimed at removing waste and eliminating bottlenecks from inefficient tools, equipment, or resources in the workplace. The five steps used are Seiri (Sort), Seiton (Set In Order), Seiso (Shine), Seiketsu (Standardize), and Shitsuke (Sustain).
E. Kaizen (Continuous Improvement)
The Kaizen technique is a powerful strategy that powers a continuous engine for business improvement. It is the practice continuously monitoring, identifying, and executing improvements. This is a particularly useful practice for the manufacturing sector. Collective and ongoing improvements ensure a reduction in waste, as well as immediate change whenever the smallest inefficiency is observed.
F. Benchmarking
Benchmarking is the technique that employs a set standard of measurement. It involves making comparisons with other businesses to gain an independent appraisal of the given situation. Benchmarking may involve comparing important processes or departments within a business (internal benchmarking), comparing similar work areas or functions with industry leaders (functional benchmarking), or comparing similar products and services with that of competitors (competitive benchmarking).
G. Poka-yoke (Mistake Proofing)
This technique’s name comes from the Japanese phrase meaning “to avoid errors,” and entails preventing the chance of mistakes from occurring. In the poka-yoke technique, employees spot and remove inefficiencies and human errors during the manufacturing process.
H. Value Stream Mapping
The value stream mapping technique charts the current flow of materials and information to design a future project. The objective is to remove waste and inefficiencies in the value stream and create leaner operations. It identifies seven different types of waste and three types of waste removal operations.
The Six Sigma Tools
- Cause and Effect Analysis
- Flow Chart
- Pareto Chart
- Histogram
- Check Sheet
- Scatter Plot
- Control Chart
Levels of Six Sigma
Overall, Six Sigma offers various career opportunities with competitive salary prospects. Individuals with Six Sigma certification can expect higher salaries and better job prospects than those without certification.